We design your production line
For 30 years we have been planning and engineering production lines with a focus on finger jointing lines. We respond to the individual needs and wishes of our customers. With holistic solutions or the renewal of individual components, old and new are combined.
For more information, please contact us at any time for a personal meeting.
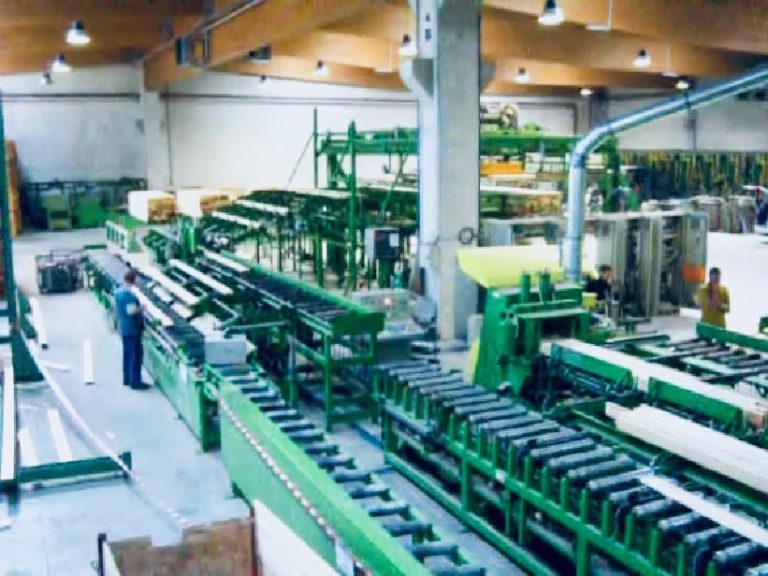
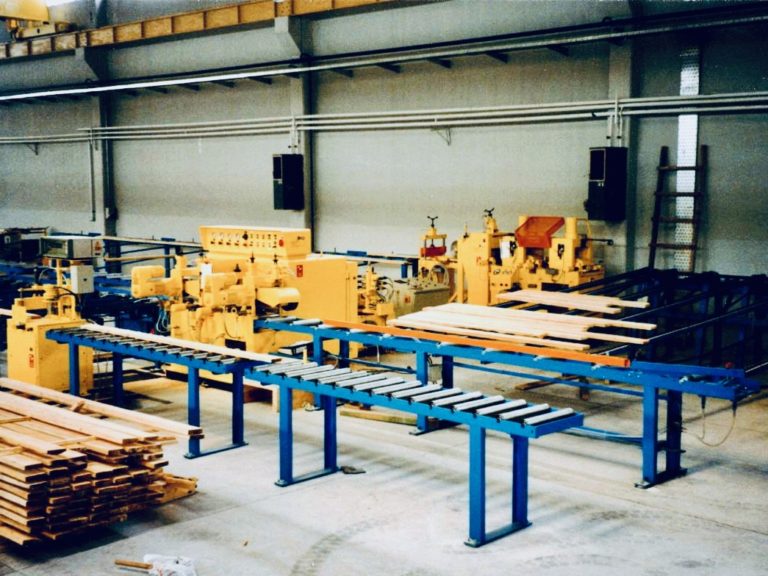
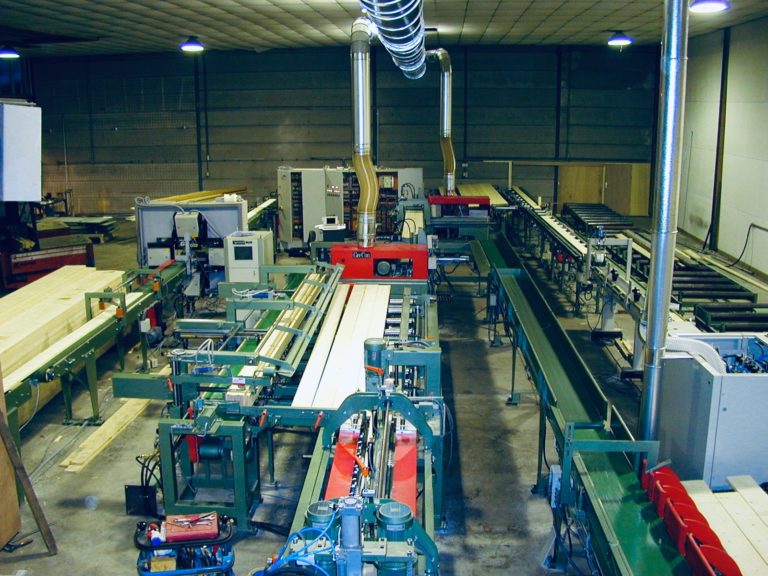
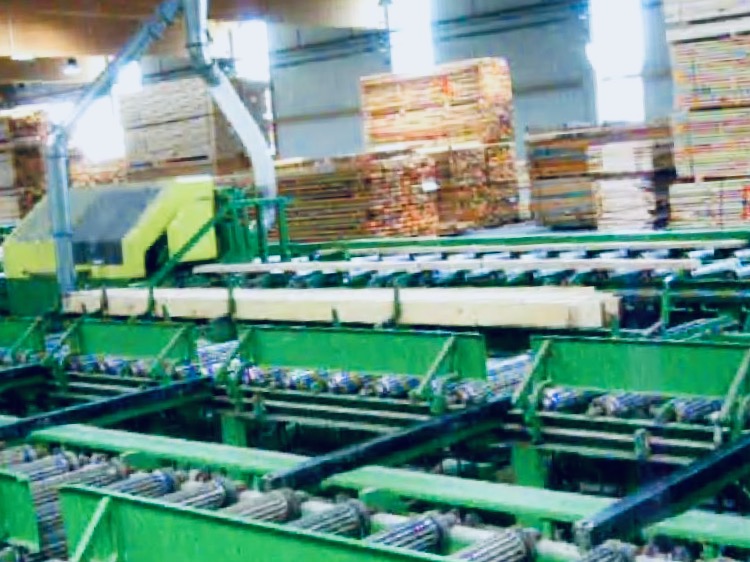
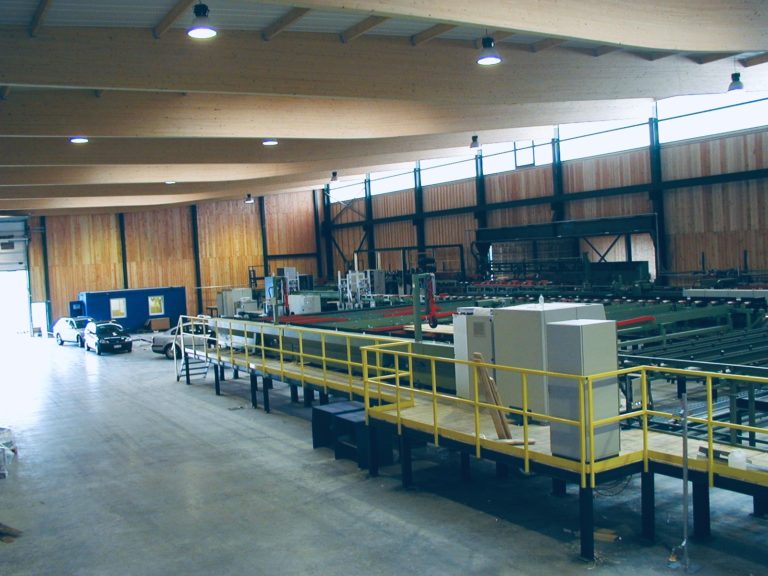
MACH I - the start of a new finger jointing era
jöma MACH I (Pat. Pending) High performance finger jointing line for solid wood, glulam, KVH, Duolam and Triolam production
Funded by the Federal Ministry of Economics and Technology on the basis of a resolution of the German Bundestag
"New finger jointing machine - Two patents pending for parcel transport "
"New finger jointing line - 100% safety guaranteed".
"Quiet and robust finger jointing - Shuttle brings high performance to package plant".
"72 Finger Joints in 60 Seconds".
"Stoic zinc - package wedge zinc plants can not be broken".
The heart of the line is the central milling and gluing machine with infeed and outfeed mechanization for bundle widths from 1 single piece up to max. 1,100 mm. Central milling in “normal version” has existed for more than 20 years and has, among other things, the advantage that the wood rests while the machine moves. Wood manipulation is easier, speeds are achieved more quickly. Our new development in the field of milling mechanization is based on the proven technology of the central milling machine. The wood is fed by a new type of high-speed package shuttle. The bundles of wood aligned in the bundling system are transported with absolute precision, so that the previously known error-prone alignment at the jolting stop in the milling machine is completely eliminated. In addition, when the timber package passes through to the 2nd milling pass, the package is simultaneously aligned with the opposite timber edge. This gives the milling performance a quantum leap upwards and at the same time significantly increases the functional reliability.
Together with new developments in the clamping stations and the transfer channel on the milling carriage, the jöma MACH I has the following groundbreaking advantages:
High cycle speed
Together with the 1,100 mm wide milling channel at 45 mm lumber thickness, this results in a technical running meter performance in the range of 150 Ifdm/min
- Extremely robust and reliable material transport
- Extensive elimination of failure-prone conveyor rollers, flaps + cross conveyor sections and thus a very high availability of the plant
- For all cross sections incl. square suitable
- Due to fully automatic, continuous channel adjustment, individual milling is also possible in extreme cases. This makes the plant extremely flexible.
The press concept after the milling machine consists of cycle presses
Cycle presses have the following advantages over other systems:
- Absolutely reliable pressing. Practically no wood breakage such as with extrusion and head presses
- Tine misalignment in width and height almost eliminated
- High flexibility with very short setup time
- Unbeatable high availability
- By adding further presses, capacity can be scaled up
A newly developed press feeder (Pat. Pending)
Extremely fast and reliable transport of the milled and glued wood behind the milling machine to the presses.
All other press systems can be connected to the MACH I as well
Wood input lengths 900 – 6.100 mm
vertical und horizontal tine profiles possible
Performance examples for vertical milling
KVH 160 x 280 mm = 12 timber parts x 4.0 m = 48 lfm/min x performance factor 0,8 = 38,4
KVH 100 x 300 mm = 20 timber parts x 4.0 m = 80 lfm/min x performance factor 0,8 = 64,0
BSH 45 x 250 mm = 40 timber parts x 3,5 m = 140 lfm/min x performance factor 0,8 = 112,0
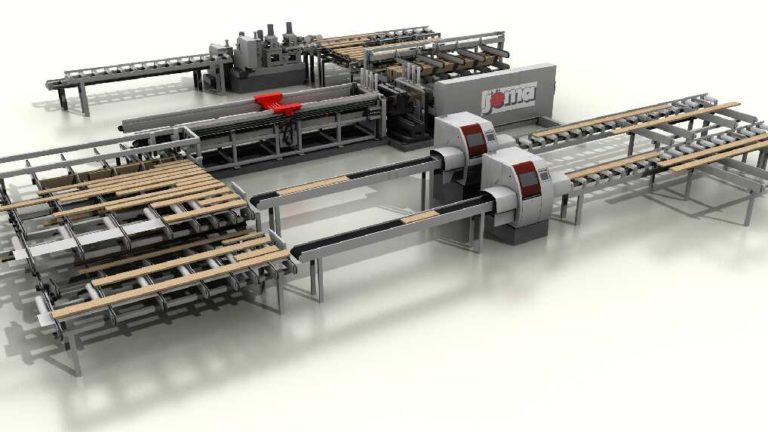
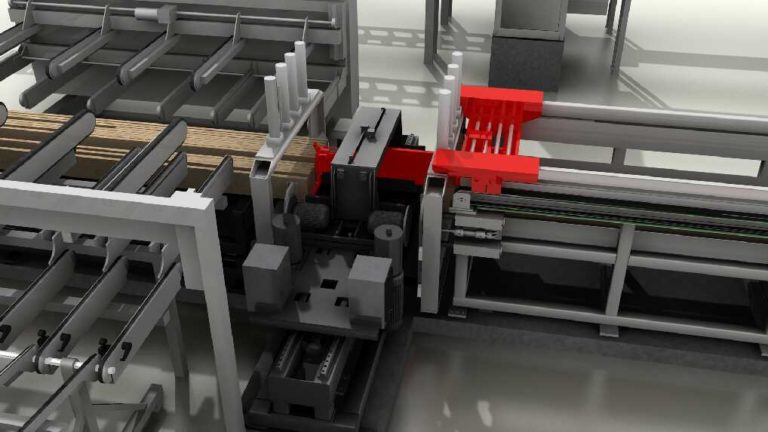
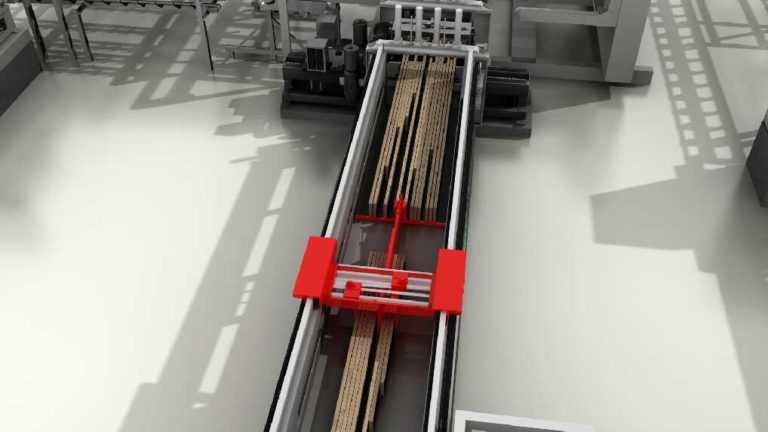
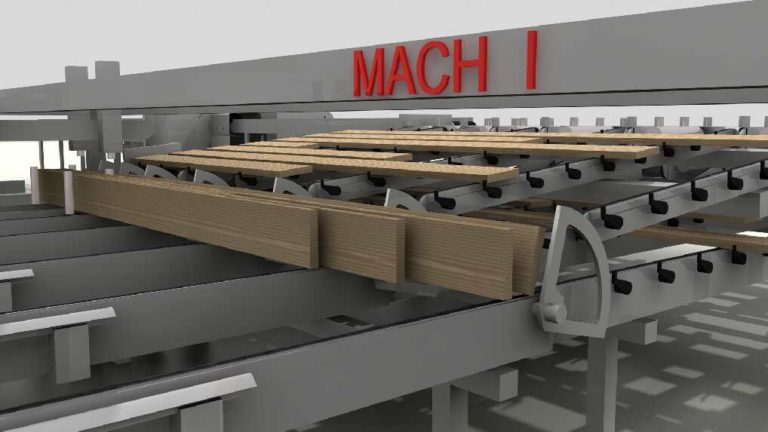